分享到微信朋友圈x
打开微信,点击底部的“发现”,
使用“扫一扫”即可将网页分享至朋友圈。
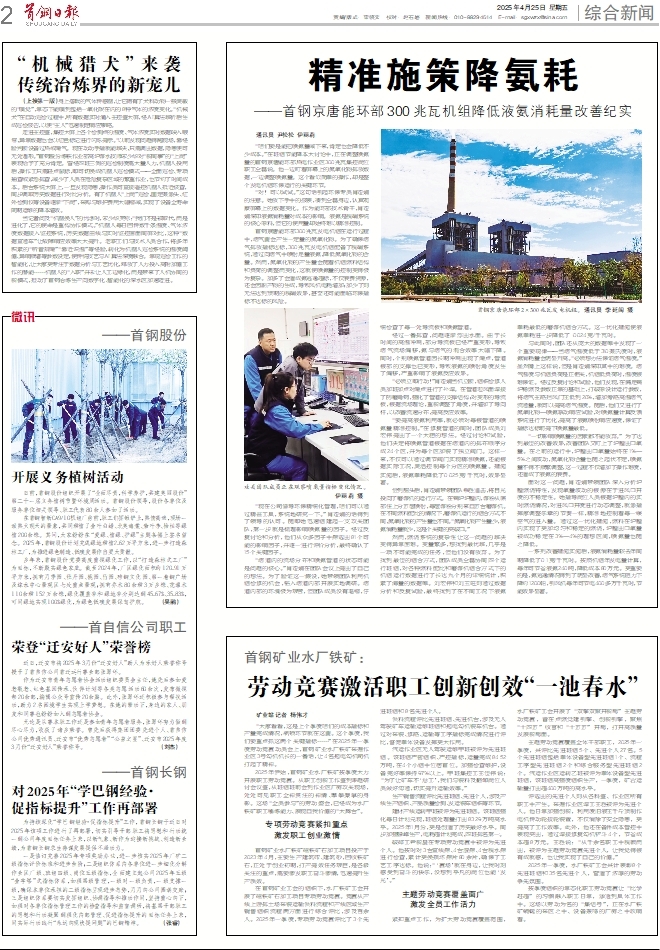
- 返回目录
- 上一篇
- 下一篇
- 放大+
- 缩小-
- 常规
精准施策降氨耗
——首钢京唐能环部300兆瓦机组降低液氨消耗量改善纪实
![]() |
首钢京唐能环部2×300兆瓦发电机组。 |
![]() |
攻关团队成员正在观察喷氨量指标变化情况。 |
“咱们要是能把喷氨量减下来,肯定也会降低不少成本。”在班组节能降本大讨论中,正在调整喷氨量的首钢京唐能环部热电作业区300兆瓦集控岗位职工仝磊说。他一边盯着屏幕上的氮氧化物排放数据,一边调整喷氨量。这个看似简单的操作,却是整个发电机组环保运行的关键环节。
“对!可以试试。”这句话引起环保专员肖连娟的注意。她放下手中的报表,凑到仝磊身边,认真观察屏幕上的数据变化。作为能环部技术骨干,肖连娟深知液氨消耗量对成本的影响。液氨是脱硝系统的核心原料,但它的使用量却始终难以精准控制。
首钢京唐能环部300兆瓦发电机组在运行过程中,烟气里会产生一定量的氮氧化物。为了确保烟气排放指标达标,300兆瓦发电机组配备了脱硝系统,通过向烟气中喷射足量液氨,降低氮氧化物的含量。然而,氮氧化物的产生量会随着机组燃料结构和负荷的调整而变化,这就使喷氨量的控制变得极为复杂。加多了会造成氨逃逸超标,不仅浪费资源,还会因副产物的生成,导致风机电耗增加;加少了则无法达到预期的脱硝效果,甚至还可能面临环保指标不达标的风险。
“现在公司倡导环保精细化管理,咱们可以通过精益工具,系统地研究一下。”肖连娟的话得到了领导的认可。随即她迅速组建起一支攻关团队,第一步就是梳理影响喷氨量的因子。经过反复讨论和分析,他们从众多因子中筛选出81个可能的影响因子,并逐一进行评价分析,最终确认了15个关键因子。
“烟道内的流场分布和喷氨管道的状态可能是问题的核心。”肖连娟在团队会议上提出了自己的想法。为了验证这一假设,她带领团队利用机组检修的机会,钻入烟道内部开展实地调研。烟道内部的环境极为艰苦,但团队成员没有退缩,仔细检查了每一处导流板和喷氨管道。
经过一番排查,问题逐渐浮出水面。由于长时间的高温冲刷,部分导流板已经严重变形,导致烟气流场偏移,氨与烟气的混合效率大幅下降。同时,个别喷氨管道因长期冲刷出现了漏点,管道根部的支撑也已变形,导致液氨的喷射角度发生了偏移,严重影响了液氨反应效果。
“必须立即行动!”肖连娟当机立断,组织检修人员加班加点对漏点进行了补焊。在管道迎风面焊接了防磨角钢,强化了管道的支撑结构;对变形的导流板,根据流场理论,重新调整了角度,并增加了导向杆,以改善流速分布,提高反应效率。
“要提高液氨利用率,就必须对每根管道的喷氨量精准控制。”在修复管道的同时,团队成员刘宏伟提出了一个大胆的想法。经过讨论和试验,他们决定将喷氨管道根据在烟道内的排布顺序分成24个区,并为每个区加装了独立阀门。这样一来,不仅可以通过调节阀门实现精准喷氨,还能根据实际工况,灵活控制每个分区的喷氨量。措施实施后,液氨单耗降低了0.025克/千瓦时,效果显著。
尝到甜头后,肖连娟带领团队乘胜追击,将目光投向了磨煤机的运行方式。在锅炉炉膛内,煤粉从底部往上分五层喷射,每层煤粉分别来自五台磨煤机。在不同燃料配比的情况下,磨煤机运行的组合方式不同,氮氧化物的产生量也不同。“氮氧化物产生量少,液氨消耗量就少,这是个关键的突破口。”
然而,燃烧系统的复杂性让这一问题的解决变得异常困难。变量繁多,想找到最优解,几乎是一项不可能完成的任务,但他们没有放弃。为了找到最佳的组合方式,团队成员仝磊协同四个运行班组,对各种燃料配比和磨煤机组合方式下的机组运行数据进行了长达九个月的详细统计,积累了海量的数据库。刘宏伟和刘玉旺则通过数据分析和反复试验,最终找到了在不同工况下液氨单耗最低的磨煤机组合方式。这一优化措施使液氨单耗进一步降低了0.024克/千瓦时。
与此同时,团队还从庞大的数据库中发现了一个重要规律——当烟气温度低于310摄氏度时,液氨消耗量会明显升高。“必须想办法保证烟气温度。”虽然嘴上这样说,但是肖连娟深知其中的难度。烟气温度与机组负荷是正相关,机组低负荷时,温度很难保证。经过反复讨论和试验,他们发现,在满足锅炉稳燃及参数正常的基础上,打破原设计运行参数,将烟气主路挡风门压低到20%,增加旁路高温烟气流通量,就可以提高烟气温度。随后,他们又进行了氮氧化物—喷氨联动响应试验,对喷氨量计算反馈系统进行了优化,提高了液氨喷射响应速度,保证了指标达标前提下喷氨量最低。
“一切影响喷氨量的因素都不能放弃。” 为了达到最佳的改善效果,改善团队又盯上了炉膛出口氧量。在之前的运行中,炉膛出口氧量始终在1%—5%之间波动,氮氧化物含量也随之起伏不定,喷氨量不得不频繁调整,这一过程不仅增加了操作难度,还造成了液氨的浪费。
面对这一问题,肖连娟带领团队深入分析炉膛燃烧特性,发现氧量波动的根源在于进风口开度的不稳定性。她指导岗位人员根据炉膛内的实时燃烧情况,对进风口开度进行动态调整,就像指挥家调整乐章的节奏一样,精准地控制着每一缕空气的进入量。通过这一优化措施,燃料在炉膛内实现了更加均匀和稳定的燃烧,炉膛出口氧量被成功稳定在3%—4%的理想区间,喷氨量也随之降低。
一系列改善措施实施后,液氨消耗量较去年同期降低了0.1克/千瓦时。按照机组年发电量计算,每年可节省液氨240吨,降低成本80万元。更重要的是,氨逃逸情况得到了明显改善,烟气系统阻力下降约1200帕,引风机每年可节电400多万千瓦时,节能效果显著。